And the robot hand became subtle and sensitive thanks to additive manufacturing
When our client asked us to industrialise this part and we studied its special morphology, we immediately understood that we were going to have a problem removing the robot from its mould: it could easily be damaged. However, we created a specific 3D piece and obtained a fast, efficient and really simple solution. This is the story.
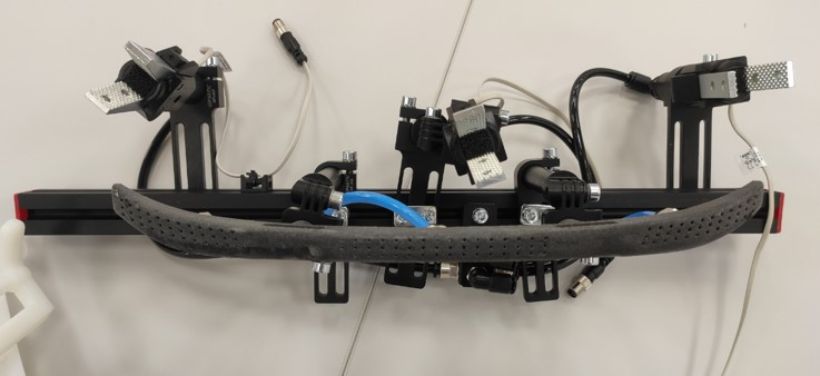
The part that our client wanted us to industrialise with ABS injection has a highly-unique morphology. Despite that, the production phase in itself was absolutely no problem for us. However, where we did quickly run into a problem was with extracting it from the mould. The task is normally done by a robotic arm that extends its hand for extraction. But, in this case the operation would be difficult due to the small surface area of the part. The problem? The suckers that are usually employed for this could not access the surface of the newly-moulded part and, the other common option, to use clamps, could damage the still hot polymer.
A faster, more effective and simpler solution
At this point, the most common response would have been to redesign the robot hand. Meaning: rethinking access to the produced product, ordering new parts to build the tool and reprogramming the entire piece, which (almost certainly) would have multiplied the number of movements of the automated equipment.
However, when this challenge was on the table, we already had enough experience with additive manufacturing, so we devised a different and simpler solution: we printed a piece that adapted to the geometry of the manufactured part and added it to the robot hand. Then, causing a Venturi effect, the part could be suctioned with uniform pressure along its entire surface. With zero damages to the finished product. All so easy and subtle.
Fast responses customised to each project
This robot hand, which is the hybrid solution (standard mechanical parts joined to a material manufactured by custom 3D) shows how automation problems can be resolved. However, it is possible to go further and design specific robotic hands for each project with all the mechanisms needed, including springs, clamps and suckers. There are so many advantages here:
- With designs adapted to each project, the movements of the robotic arms can be reduced, increasing their service life.
- By using polypropylene, we reduced the weight of the hand, which improved the performance of the overall automated group.
- We can apply changes and/or corrections to the ensemble very quickly.
- Several hands can be manufactured for the same job to have replacement parts.
What we know beyond a shadow of a doubt is that – with a tool like additive manufacturing – our imaginations can soar and solutions are accelerated.
Photo1: Our 3D solution / Photo2: the hybrid robot hand / Photo3: the hand with the extracted part